Exhaust air purification is the removal of harmful constituents and components before they are discharged into the environment or atmosphere.
An exhaust air cleaning or exhaust gas cleaning system is required in order to comply with official and statutory regulations regarding the introduction of process exhaust air into the environment. In air pollution control, the terms exhaust air cleaning, exhaust gas cleaning or afterburning are often used under the same background.
Schedule line characteristics can be considered:
- The term "exhaust air" is often associated with "production" exhaust air, for example - this is usually relatively cool, usually below 100°C media temperature.
- In return, the term exhaust gas is used for warm exhaust air. The media temperature here is usually above 100°C and usually comes from heat treatment plants. Both terms have a relatively high air content in the medium.
- The term afterburning, on the other hand, is frequently used directly in the thermal treatment of raw gas or system gases, among other things, from the fields: Debinding, coking, decoating, pyrolysis, carbonisation. Common to all these processes is the generally air- or oxygen-free process gas formation, which is subsequently fed to the post-combustion plant. To simplify matters, the general term "exhaust gas" is also used for this type of process gas.
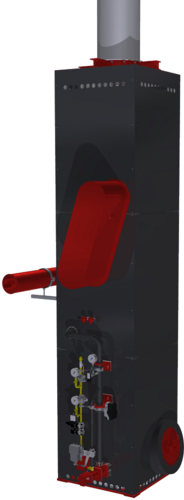
Thermal afterburning (TNV)
Thermal afterburning is an exhaust air cleaning or exhaust gas cleaning system using oxidation.
Depending on the process or clean gas requirements, working temperatures of 650...1200 °C with corresponding residence times of at least 0.7 sec. are realized in the TNV combustion chamber. Thermal post-combustion is an air-hygienically optimal process, since the exhaust air or exhaust gases, with the exception of sulphur, halogens or other thermally non-decomposable foreign substances, are completely converted into the harmless substances water (H2O) or carbon dioxide (CO2).
Areas of application and advantages:
- suitable for one VOC load >1 gC/Nm³
- VOC Separation efficiency >99.8%
- very wide range of applications
- fast starting and stopping possible
- autothermal operation with concentration above 6-8 gC/Nm³ possible
- particularly suitable for strongly fluctuating process conditions (exhaust air volume flow, pollutant concentration, temperatures, ...)
- only process for the incineration/disposal of liquid pollutants
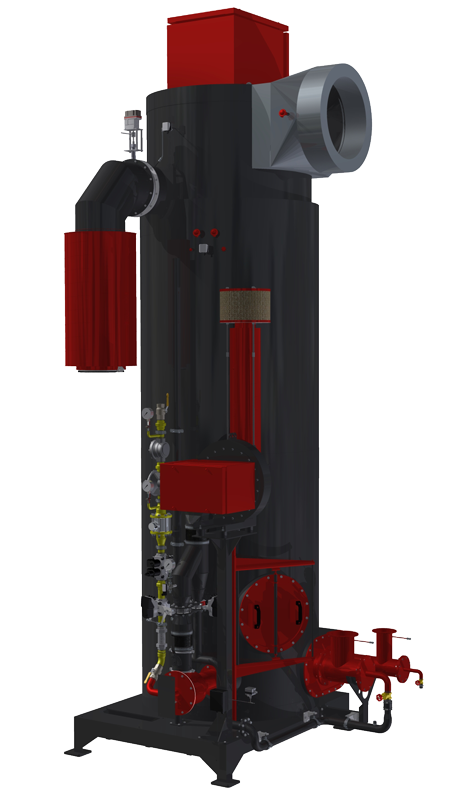
Our thermal post-combustion plants offer a great deal of potential for heat and energy recovery in order to drastically reduce the energy costs to be used.
The "thermal afterburning" process is absolutely flexible with regard to the type and composition of the exhaust air or raw gases to be introduced and can therefore be adapted to all conceivable processes.
Any oxygen content bound in the raw gases or the exhaust air does not play a role in the combustion or oxidation process starting in the post-combustion chamber. When raw gases are introduced from an inert process, the required oxygen is fed separately into the reaction chamber. When exhaust gases from an air-guided process are fed in, the required oxygen content is already contained. The exhaust gas and fuel gas are combined by means of a special combustion plant of our greenfire generation.
Thermal afterburning plants from Birk Wärmetechnische Anlagen GmbH are specially adapted to each customer process and can also be subsequently adapted or extended to other processes. They offer the possibility of the simultaneous introduction of exhaust air, as well as exhaust gases (raw gases) and liquids (condensates, etc.) - the "Birk" TNV plants are therefore often called "omnivores" by our customers.
Our TNV systems are specially designed and adapted to the customer's installation site, so that a cost-effective and effective exhaust air/flue gas cleaning can be realised even in confined and minimal space conditions.
Extract from the range of services - Thermal afterburning plants
- Compact design
- System versions for vertical, horizontal or suspended installation
- System designs for indoor or outdoor installation
- Option: Version for installation in EX zones of various categories
- Option: Version for installation in the food sector
- System installation (standing, lying, hanging,...as well as indoors or outdoors) Any
- System designs for volume flows: 10 mn³/h to 50,000 mn³/h
- Plant designs for raw gas/polluted gas mass flow: 0.5 kg/h to 1000 kg/h
- Equipment designs for mixed operation - so-called "omnivores
- over 90% energy and heat recovery possible through system combinations
- integrated and external process air preheating at the TNV combustion chamber
- Possible combinations of heat recovery for the processes:
Process air/air heaters
Warm/hot water production
steam generation
Thermal oil production and others - Firing and heating technology for gases, oils, liquids and others - as well as by means of electric heating registers
- Own efficient burner technology for the combustion plant in low NOx technology
- SNCR and SCR concepts for nitrogen oxide reduction
- Integration of a RAD adsorber for concentration and minimization of the pollutant gas flow
- Combination and delivery with desulphurisation, dedusting and other measures for the removal of non-oxidisable foreign substances possible
- Advanced technology for minimal maintenance
- Portfolio of cost-effective "standard" TNV systems in specified sizes and applications
Describe us your task - we have "guaranteed" the right solution!
Regenerative (thermal) post-combustion (RNV)
Regenerative (thermal) afterburning is an exhaust air purification system using oxidation and integrated heat recovery for process exhaust air preheating.
Depending on the process or clean gas requirements, working temperatures of 650...900 °C are achieved in the RNV combustion chamber with corresponding residence times.
Like the TNV process, regenerative afterburning is an air-hygienically optimal process, since the exhaust air is completely converted into the harmless substances water (H2O) or carbon dioxide (CO2). Regenerative post-combustion plants offer a great deal of savings potential through integrated heat and energy recovery for the process air, whereby the energy costs to be used are minimised or, in autothermal processes, reduced to the use of electrical energy.
The "regenerative afterburning" process is particularly recommended for higher exhaust air volume flows and for processes in which no further generation of process heat (warm/hot water, thermal oil, steam) is required. Our regenerative post-combustion plants are specially adapted to each customer process and can also be subsequently adapted or extended to other processes. Our RNV plants are specially designed and adapted to the customer's installation site, whereby a cost-effective and effective exhaust air cleaning can be realised even in confined and minimal space conditions.
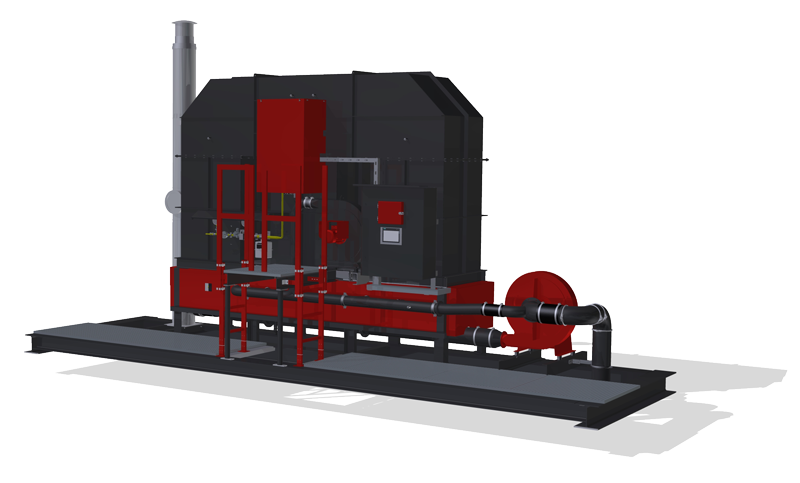
Possible and recommended areas of application for an RNV system:
- Chemical Processes
- coating processes
- painting processes
- Printing and packaging industry
- paper industry
- food industry
- surface treatment
- wood industry
- odor elimination
Extract from the range of services
Regenerative afterburning plants
- Compact design
- System designs for indoor or outdoor installation
- Option: Version for installation in the food sector
- System designs for volume flows: 1,000 mn³/h to 50,000 mn³/h (higher volume flows on request)
- highest energy and heat recovery respectively autothermal processes
- Combination options for further heat recovery:
Process air/air heater
Warm/hot water production Thermal oil production and others
- Own efficient burner technology for the combustion plant in low NOx technology
- Integration of a RAD adsorber for concentration and minimization of the pollutant gas flow
- Advanced technology for minimal maintenance
- Portfolio of cost-effective "standard" RNV systems in specified sizes and applications
Catalytic afterburning (KNV)
Catalytic afterburning is an exhaust air purification system using oxidation. By using appropriate catalysts, the reaction temperature of the exhaust air components is considerably reduced in this process.
Depending on the process or clean gas requirements, working temperatures of 250...400 °C with corresponding residence times are realized in the KNV reaction chamber.
Catalytic post-combustion plants offer a lot of savings potential due to the lower demand for additional fuel via the reaction chamber heating, whereby the energy costs to be used are minimised. Autothermal processes can be implemented even at the lowest pollutant concentrations. The "catalytic post-combustion" process is particularly recommended for exhaust air volume flows from the surface industry, furniture production, painting technology, the food and plastics industries or comparable applications. Our catalytic post-combustion plants are specially adapted to each customer process and can also be retrofitted or extended to other processes.
Our KNV systems are specially designed and adapted to the customer's installation site, which enables cost-effective and effective exhaust air purification even in confined and minimal space conditions.
Extract from the range of services
Catalytic afterburners
- Compact design
- System designs for indoor or outdoor installation
- Option: Version for installation in the food sector
- System designs for volume flows: 1,000 mn³/h to 50,000 mn³/h (higher volume flows on request)
- high internal heat utilisation (up to 85%) or autothermal processes
- Possible combinations for further heat recovery:
Process air/air heater
Warm/hot water production
steam generation
Thermal oil production and others - Own efficient burner technology for the combustion plant in low NOx technology
- Advanced technology for minimal maintenance
- Portfolio of cost-effective "standard" KNV systems in specified sizes and applications
Describe us your task - we have "guaranteed" the right solution!